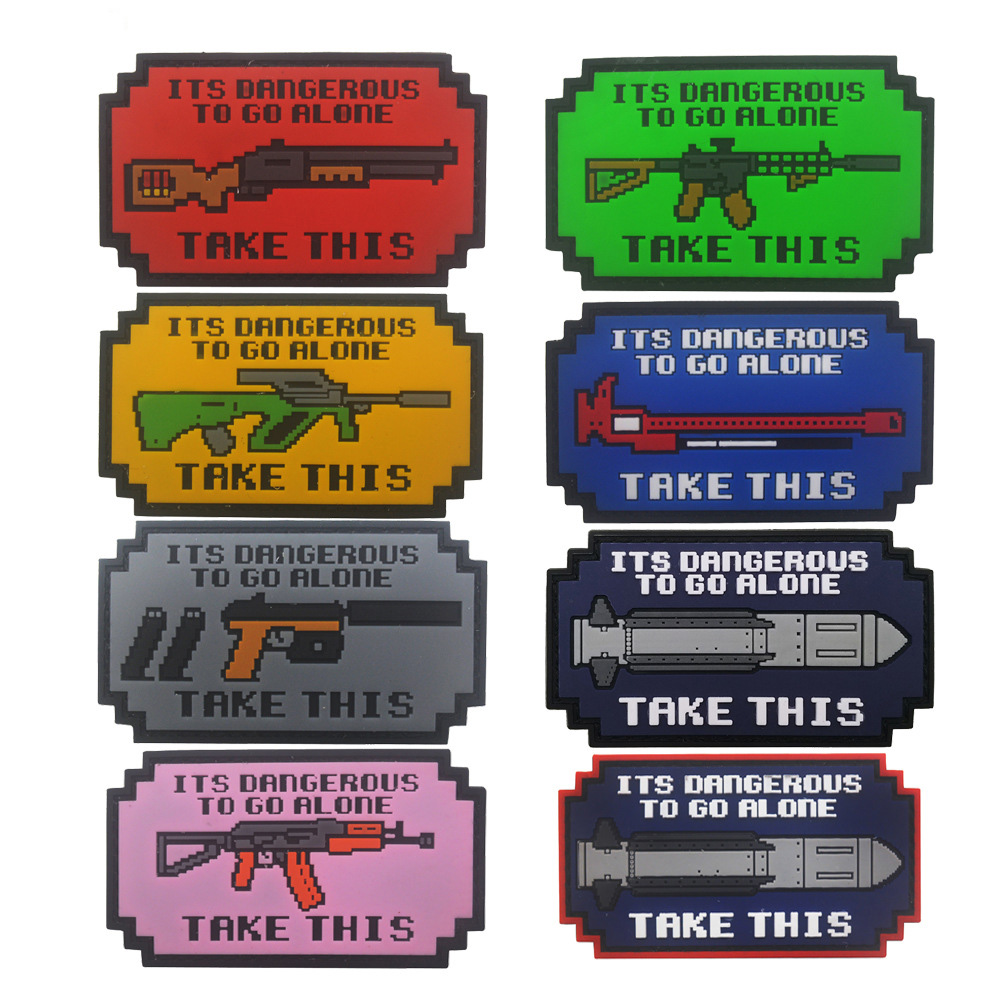
First, Rubber Flying Edge The Existence Of Flying Edge Has Many Bad Effects On The Production Process And Quality Of Rubber Products. 1) The Design Of Products Is Generally Not Allowed To Appear Flying Edge, From The Perspective Of Quality Requirements Must Be Repaired. Trimming The Flying Edge Requires A Lot Of Manpower And Space, Which Virtually Adds A Process And Prolongs The Production Cycle. From The Business Point Of View, The Repair Of The Flying Edge Increases The Production Cost. 2) The Formation Of Flying Edge Increases The Consumption Of Rubber And The Production Cost. At The Same Time, It Is A Waste Of Resources And A Potential Pollution To The Environment 3) The Formation Of The Flying Edge Changes The Sealing Size Of The Die Products, So That The Performance Of Some Products Is Affected (especially For The Strict Requirements Of All Kinds Of Sealing Products). 4) The Trimming Of Flying Edges, Especially Manual Trimming, Obviously And Seriously Affects The Apparent Quality Of Products, Thus Reducing The Commercial Value Of Products. As The Saying Goes: "goods Sell A Skin", It Is This Truth. The Traces Of The Trimmed Flying Edge Are Different And Different, Which Directly Affects The Image Of The Enterprise In The Eyes Of Customers And Makes The Enterprise Lose Its Competitiveness In The Market. For The Above Mentioned Various Negative Effects Of Flying Edge, Whether Technical Workers Or Production Organizers And Operators Should Be From The Product Quality, Corporate Image, Social Benefits And Enterprise Development Strategy Requirements From The Height Of Understanding. So. It Is Necessary To Put Forward Such A Resounding Slogan: "improve Technology, Improve Process, Move Towards Less And No Flyingization" Two, Rubber Aging The Aging Phenomenon Of Rubber Under The Condition Of Repeated Deformation Is Called Fatigue Aging. The Fatigue Aging Of Rubber Is Usually Caused By Mechanical Force, Oxidation And Ozonation. The Essence Of Rubber Fatigue Aging Is A Process Of Stress - Chemical Change. Analysis Of The Causes Of Rubber Fatigue Aging: 1) Mechanical Cracking Reaction Occurs Under The Action Of Mechanical Forces. Due To The Viscosity Of High Polymer, The Rubber In The Deformation Cycle, The Relaxation Process Is Too Late To Complete, And Then Into The Next Deformation Cycle, Resulting In Rubber Internal Deformation Residual Stress Is Increasing. When The Stress Gradient Is Large, The Molecular Chain Will Break Directly And Generate Free Radicals, Which Leads To The Oxidation Chain Reaction Of Rubber Molecules. 2) Under The Action Of Mechanical Force, The Oxidative Cracking Reaction Of Mechanical Activation Is Generated. When Rubber Is Repeatedly Deformed, Its Mechanical Stress Will Weaken The Valence Force In The Rubber Molecular Chain, Thus Reducing Its Oxidation Activation Energy. Thus, The Oxidative Cracking Reaction Of Rubber Molecules Was Accelerated. The Reduction Of Oxidation Activation Energy Is The End Of The Conversion Of Mechanical Energy Into Chemical Energy In The Fatigue Process. 3) Under The Action Of Mechanical Force, The Heat Generated Inside The Rubber Accelerates The Oxidation Reaction. When The Rubber Is Repeatedly Deformed, The Hysteresis Phenomenon Occurs, Causing Internal Friction, Which Makes The Rubber Generate Heat Inside, And Accelerates The Oxidation Chain Reaction Of The Rubber. 4) In The Process Of Fatigue, The Ozone Cracking Of Rubber Is Accelerated. In The Fatigue Aging Process Of Rubber With Periodic Deformation, Ozone Cracking Phenomenon Appears, And This Phenomenon Is More Significant At High Temperature. For Example, The Cracking On The Surface Of High-speed Car Tires Is The Result Of Ozone Aging In The Process Of Fatigue. The Protection Of Rubber Fatigue Aging Is To Add A Flexor-cracking Inhibitor To The Rubber Material, Whose Main Function Is To Improve The Stability Of Rubber Structural Changes In The Fatigue Process, Especially Under High Temperature Conditions, This Inhibitor Can Slow Down The Oxidation Reaction And Ozonation Reaction Caused By Stress Activation. Effective Inhibitors Are Mostly Condensation Of Ketones And Aromatic Amines (such As Aw, Ble, Etc.) And Antiaging Agents Of P-phenylenediamines. In The Formulation Design Of The Compound, The Combination Of Antioxidant And Anti-ozone Agent Is Often Used, Which Will Also Produce A Good Effect On The Protection Of Fatigue And Aging. Three, Rubber Fracture Characteristics In The Process Of Rubber Processing, Its Rheological Properties Are Mainly The Viscosity, Elastic Memory And Mechanical Properties Of Rubber In The Process Of Fracture, Referred To As Fracture Properties. From The Essence Of Rubber Material, The Change Of The Machinability Is Mainly Due To The Relative Molecular Weight Of The Rubber, The Relative Molecular Weight Distribution And The Result Of The Branching Of Long Chain. So Far, People's Research On Rubber Fracture Characteristics Mainly Focuses On The Process Of Rubber Mixing. In The Process Of Rubber Refining, There Is A Large Deformation And Small Deformation Of Rubber, So The Deformation Is Not Gentle And Stable, But There Is Yield Flow And Fracture, And The Deformation Under The Processing Conditions Often Exceeds Its Fracture Limit. Many Basic Rheological Properties Of Rubber Compound Could Not Explain The Fracture Characteristics Of Raw Rubber, So The Terms "cheesy" And "rubbery" Were Used To Describe The Fracture Characteristics. According To Experience, "cheesy" Or "broken Wadding" Rubber Material Is Difficult To Plasticize And Mix, Carbon Black Reinforcing - Filling Agent Is Not Easy To Decompose. Some Views Believe That Rubber With Good Processing Properties Should Be A Proper Combination Of Plasticity And Elasticity. Although People Have Done A Lot Of Fracture Analysis On Vulcanized Rubber, But Few People To Raw Rubber Fracture Analysis. In Foreign Countries, To Kita Et Al. Made A Very Important Study On The Fracture Process Of Raw Rubber From The Point Of View Of Mechanics, And Related The Fracture Characteristics To The Processing Properties And Molecular Structure Characteristics Of Raw Rubber. In Short, The Fracture Characteristics Of Raw Rubber Are Mainly Elongation At Break, Elasticity And Plasticity. In The Industrial Application Of Rubber, The Tensile Strength And Elongation At Break Of Raw Rubber Were Measured To Characterize Its Fracture Process. The Fracture Characteristics Of Rubber And Its Molecular Structure Have The Following Relationship: The Relative Molecular Mass Distribution Is Wide, Its Processing Technology Is Good; If The Relative Molecular Mass Distribution Is Narrow, Then The Elasticity Increases As The Relative Molecular Mass Increases. This Is Dry For Rubber, No Viscosity, Will Be Pressed Into Pieces And Slag At The Roller Distance Of The Rubber Mixer, It Is Difficult To Process; When The Branching Degree Of Molecular Chain Increases, The Elasticity Increases And The Processing Is Difficult. It Can Be Said That The Relative Molecular Weight Of Rubber, The Relative Molecular Weight Distribution And The Degree Of Molecular Chain Branching Are The Main Factors Affecting The Fracture Characteristics Of Raw Rubber, And The Fracture Characteristics Are The Main Factors Affecting The Processing Properties Of Rubber Smelting.